Rubber Expansion Joint: Protecting Equipment from Vibration and Thermal Movements
- Flexatherm Solutions
- Jun 7, 2024
- 4 min read
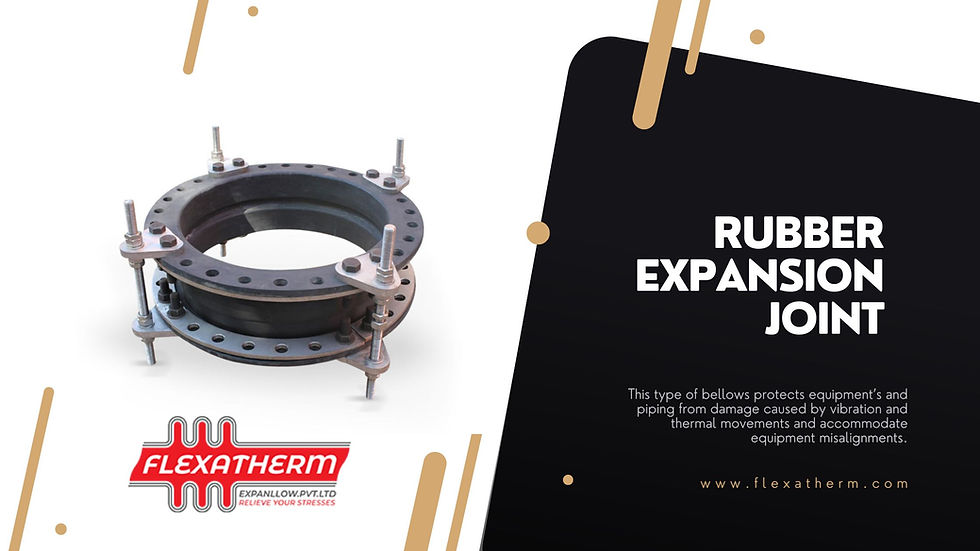
Rubber expansion joints are crucial parts of many industrial applications. They can accept misaligned equipment and shield pipes and equipment from thermal movements and vibration damage. Rubber expansion joints are well-known for their exceptional flexibility, absorption of movement, and cycle life. They are also resistant to abrasion and chemical attack. Because of their versatility in a broad range of temperatures and pressures, they are the material of choice for many applications involving liquids, slurries, gases, and solids.
What is a Rubber Expansion Joint?
A rubber expansion joint is a flexible joint made of textiles and elastomers, either synthetic or natural. Metal and other reinforcing materials may also be a part of it. These joints are made to accommodate misalignment, mechanical vibration, and thermal expansion in pipe systems.
Key Components
Bellows: The pliable component that permits mobility.
Flanges: Attach the pipe system to the expansion joint.
Reinforcement: Materials with increased strength and endurance, such as metal rings or wires.
Types of Rubber Expansion Joints
Single Arch Expansion Joints
These are the most prevalent kind, with a single bellow that may be bent in several ways.
Multiple Arch Expansion Joints
These can absorb more movement and have more flexibility because they contain several bellows.
Tapered Expansion Joints
intended to join pipes with varying diameters, guaranteeing a seamless flow across various sizes.
Offset Expansion Joints
These connections offer a way to solve non-linear configurations by accommodating misaligned pipe systems.
Key Features of Rubber Expansion Joints
Flexibility
Excellent flexibility is provided by rubber expansion joints, which is essential for absorbing movement and lessening strain on piping systems.
Movement Absorption
They can safeguard the system against thermal expansion and contraction by absorbing large quantities of movement, including axial, lateral, and rotational movements.
Cycle Life
These joints are a sturdy option for industrial applications because of their extended cycle life.
Chemical Resistance
Rubber expansion joints can be used in tough chemical conditions because they are resistant to chemical attack.
Abrasion Resistance
They are resistant to abrasive materials, thus they will last under tough circumstances.
Applications of Rubber Expansion Joints
HVAC Systems
utilized in HVAC (heating, ventilation, and air conditioning) systems to absorb vibration and thermal expansion.
Water and Wastewater Treatment
They control the flow and alignment of water and wastewater piping systems.
Chemical Processing
In chemical processing plants, rubber expansion joints withstand high temperatures and strong chemicals.
Power Generation
used in power plants to control thermal movements and lessen pipe vibration.
Pulp and Paper Industry
They make room for the flow of slurry and other products in the pulp and paper industry's transportation networks.
Advantages of Using Rubber Expansion Joints
Protection Against Vibration
Rubber expansion joints lessen the vibration that is transferred from machinery to pipes, protecting the system and extending its lifespan.
Handling Thermal Movements
By efficiently absorbing heat expansion and contraction, they safeguard the piping system's structural integrity.
Accommodating Misalignments
These joints offer flexibility during installation and operation by accommodating small misalignments in pipe systems.
Versatility in Temperature and Pressure Ranges
Rubber expansion joints are adaptable to a variety of applications because they can withstand a broad range of pressures and temperatures.
Materials Used in Rubber Expansion Joints
Natural Rubber
Excellent tensile strength and flexibility make it appropriate for a wide range of general applications.
Neoprene
Neoprene is perfect for usage in areas where these compounds are present because it is resistant to oils and solvents.
EPDM
EPDM is frequently utilized in outdoor applications because of its exceptional resilience to heat, ozone, and weather.
Nitrile
Its exceptional resistance to oils qualifies it for use in petrochemical applications.
Hypalon
employed in harsh chemical conditions, providing exceptional durability and chemical resistance.
How Rubber Expansion Joints Work
Mechanism of Movement Absorption
Rubber expansion joints are designed to withstand mechanical vibrations and temperature fluctuations by compressing and expanding their flexible bellows.
Role in Vibration Dampening
They guard against wear and tear by reducing the vibration that pumps and other equipment transmit to the piping system.
Handling Pressure Variations
Pressure variations may be accommodated by these joints, guaranteeing the stability and security of the system.
Installation and Maintenance Tips
Proper Installation Procedures
To prevent stress and early failure, make sure everything is aligned correctly and adhere to manufacturer instructions.
Regular Inspection and Maintenance
To prolong the life of the joint, regularly check for indications of wear, cracks, or leaks and carry out any necessary repair.
Common Issues and Troubleshooting
To tackle typical issues such as misalignment, excessive pressure, and chemical assault, adhere to industry best practices and manufacturer guidelines.
Industry Standards and Certifications
Relevant Standards (e.g., ASTM, ISO)
Rubber expansion joints are made with quality and dependability in mind when industry standards are followed.
Importance of Certifications
Joints that have certifications from reputable organizations are guaranteed to meet strict performance and safety standards.
Challenges and Solutions in Using Rubber Expansion Joints
Common Challenges Faced
Performance can be impacted by things like mechanical wear, exposure to high temperatures, and chemical deterioration.
Practical Solutions and Best Practices
These difficulties can be lessened by selecting the appropriate material, installing it correctly, and performing routine maintenance.
Comparison with Other Types of Expansion Joints
Rubber vs. Metal Expansion Joints
Metal joints can withstand higher pressures and temperatures, while rubber joints are more flexible and resistant to chemicals.
Rubber vs. PTFE Expansion Joints
Rubber joints are more adaptable and affordable for a larger range of applications, but PTFE joints are great for extremely corrosive conditions.
Future Trends in Rubber Expansion Joints
Technological Advancements
Rubber expansion joints are more durable and function better thanks to material and design innovations.
Emerging Materials
The creation of novel composites and elastomers increases their resilience to harsh environments.
Industry Demands
Innovation and quality enhancements are fueled by the growing need for dependable and durable expansion joints.
Case Studies and Real-World Examples
Examples from Various Industries
showcasing effective uses in water treatment, chemical processing, and power production.
Success Stories and Lessons Learned
Acquiring knowledge from practical applications to enhance subsequent undertakings.
Rubber expansion joints, which provide flexibility, chemical resistance, and movement absorption, are essential in today's business. They provide endurance and dependability in a variety of applications by safeguarding machinery and pipe systems. Through an awareness of these joints' properties, applications, and maintenance requirements, industries may make the most out of them. To know more please visit flexatherm

Comments